
Online Vocational training course on design, manufacture and validation of custommade orthopaedic, oral and cranio-maxillofacial devices (OVOMAX)
Objetivos
Nowadays, surgeons demand for medical devices highly adapted to patients needs. In some cases, standard implants are not sufficient because of abnormal anatomy or postoperative complications.
As an example, in a recent study, it was concluded that younger patients have a lower success rate than older patients when standard implant components are used. Fully customization of medical devices enables greater structural, functional and biological biocompatibility with the patient, enabling longer implant life-times; improved aesthetics, performance and patient comfort leading to improved quality of life; and often enable quicker and less invasive surgical operations; thus demonstrating higher-added value.
Traditional fair manufacturing processes, as forging, casting or machining, require the manufacture of large product batches to streamline time and costs. This limitation of traditional manufacture processes makes unfeasible the manufacture of a single device (customized or not) or short production runs at a reasonable cost.
Advances in manufacturing processes and ushering of additive manufacturing for direct production of implants has eliminated the constraints of shape, size and internal structure and mechanical properties making it possible for the fabrication of implants that conform to the physical and mechanical requirements of the region of implantation, and thus enabling the manufacture of custom-made implants in a cost-effective manner within reasonable deadlines.
The global market for 3-D printing in medical application was valued $354.5 million worldwide in 2012 and is expected to grow at a compound annual growth rate (CAGR) of 15.4 percent from 2013 to 2019 to reach $965.5 million by 2019.
Considering that Europe dominated the additive manufacturing for medical devices market in 2012, these economic forecasts augur a promising future for those European Medical Device manufacturers that decide to incorporate design and manufacture of customized implantable devices to their portfolio. This situation will result in the incorporation of specifically trained professionals or in the training of the existing staff.
The productions process of custom-made medical devices can be summarized in three main steps:
1. Design of the medical device (CAD) from medical imaging obtained mainly by CT or MR.
2. Validation of the device. Custom-made design must be validated to assure that fulfill with the mechanical and functional requirements. This validation can be performed using numerical methods like FEM or other computational methods.
3. Manufacturing process of the device. In the case of additive manufacturing techniques, prior to start with manufacture process the CAD of the device must be adapted, incorporating the necessary support structures for the device manufacture.
As can be seen, creating custom-made medical device models requires skills that many design professionals not usually have. While many of the newer, additive manufacturing machines do not require significant skill to operate, but preparation of the files and some post-processing requirements may require more ability. Thus, training about additive manufacturing is critical during the design phase.
Empresas colaboradoras
Coordinator:INSTYTUT TECHNIKI GORNICZEJ KOMAG (KOMAG), Poland
Partners:
INSTITUTO DE BIOMECANICA (IBV), Spain
ASOCIACION DE INVESTIGACION DE LAS INDUSTRIAS METALMECANICAS, AFINES Y CONEXAS (AIMME), Spain
FEDERACIÓN ESPAÑOLA DE EMPRESAS DE TECNOLOGÍA SANITARIA (FENIN), Spain
ATEKNEA SOLUTIONS HUNGARY KFT (ATEKNEA), Hungary
Duración y referencia
Fecha de inicio: 01-09-2015
Fecha de finalización: 01-09-2018
Referencia del proyecto: Project number: 2015-1-PL01-KA202-016969
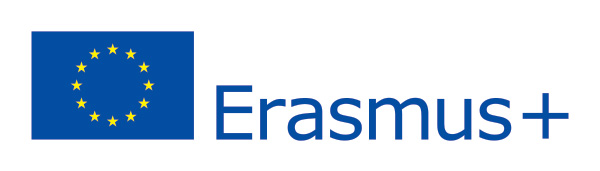
This initiative is funded by the Erasmus + program supported by the European Union.
Project number: 2015-1-PL01-KA202-016969
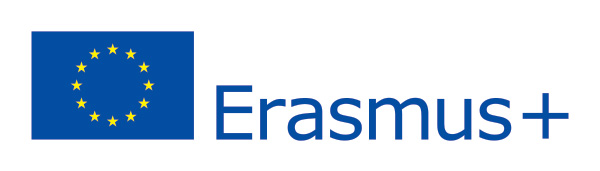